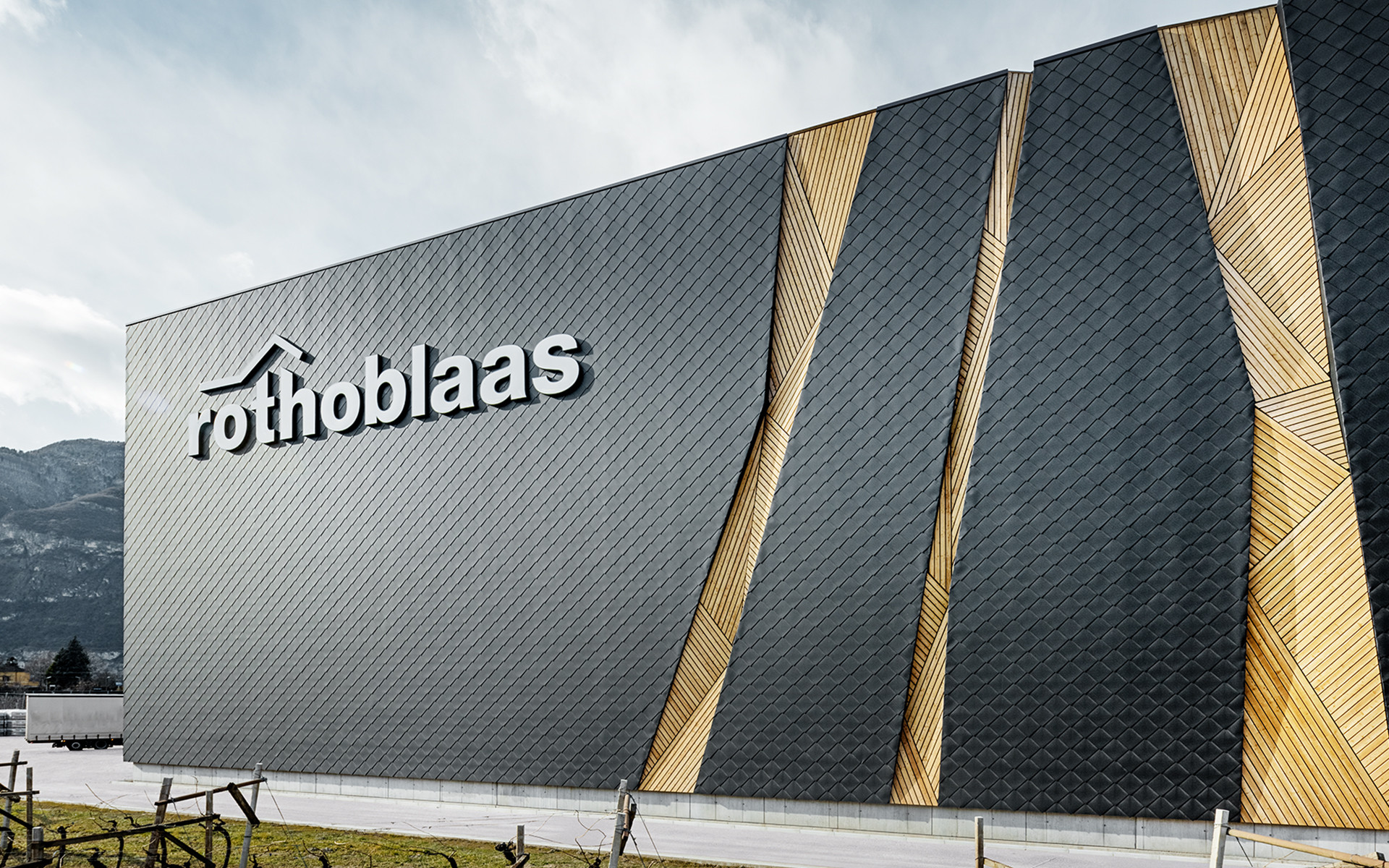
A self-supporting and automatic timber warehouse
An engineering challenge
Through new technologies, especially CLT, timber construction is crossing boundaries that were previously impassable, with buildings tens of storeys high. But the race to the sky is not the only challenge for designers. Self-supporting warehouses are advanced engineering works, in which the shelves form part of the building's load-bearing structure together with the roofing and infill elements. The shelves must therefore bear the weight of the goods stored, as well as the weight of the various building elements, together with the stresses caused by the handling equipment and external agents. Usually, moreover, the decision to build a self-supporting warehouse is associated with the installation of automation systems for pallet handling, which make it possible to manage and optimize logistics processes.
It is precisely because of all these stresses that steel is generally chosen as the structural material. The new warehouse we are talking about in this article, however, not far from the Austrian-Italian border, was made of timber, which makes it the first fully self-supporting automatic warehouse built entirely of timber in Italy and also one of the very few examples built to date in the world.
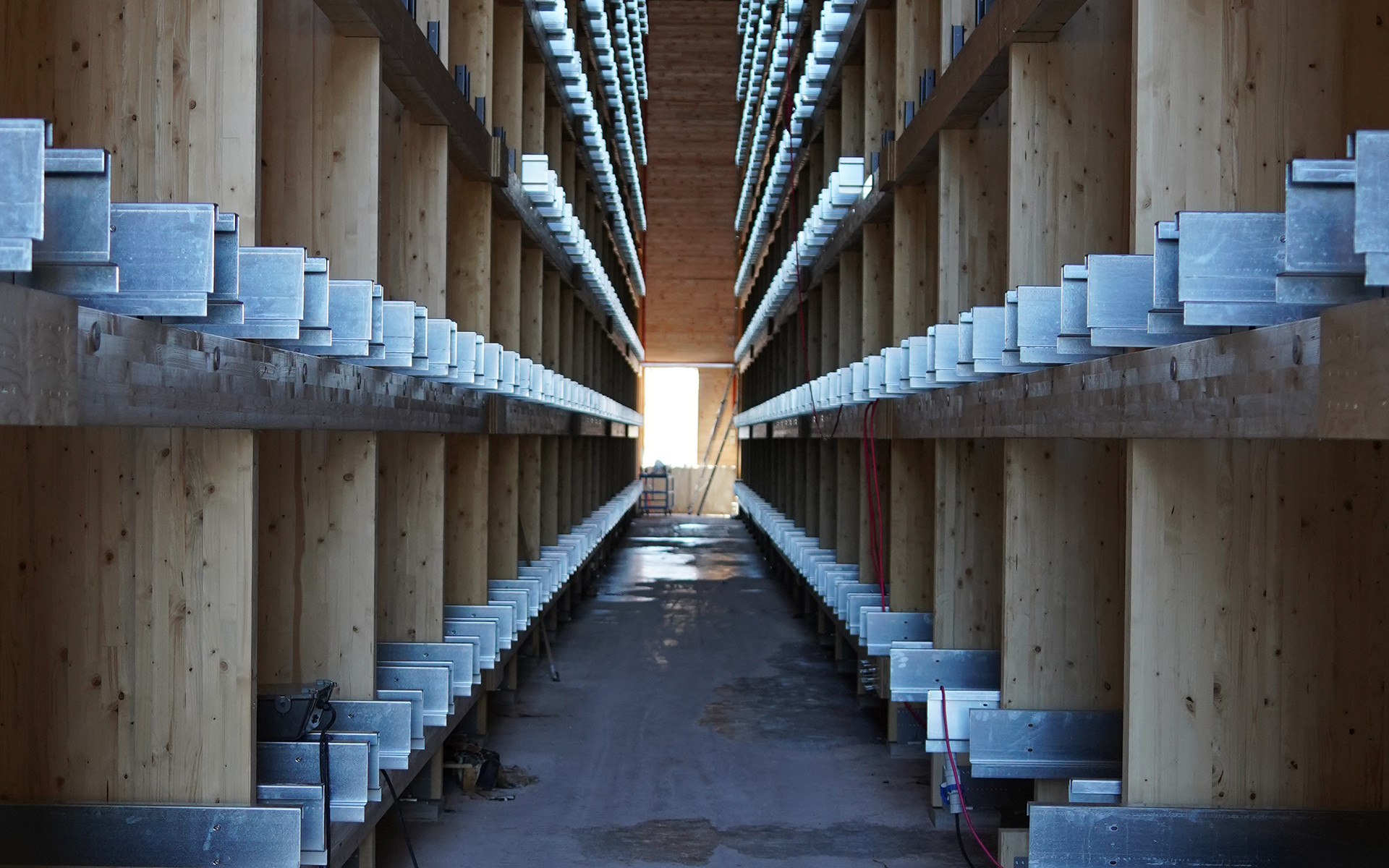
The customer
By expanding the Rothoblaas headquarters and building the new self-supporting automatic warehouse, an efficient warehouse is now available for the timely replenishment of existing warehouses and of those planned in the near future. This operation demonstrates that all kinds of constructions can now be built using timber, bringing great benefits to the environment and also to the well-being and health of the people who spend many hours a day in that building.
Architectural concept
The style behind the new warehouse and headquarters wing confirms the company's past choices, in particular the use of large windows and an important presence of timber, used both for structures and for flooring and cladding. Certain fire safety requirements, however, have imposed different solutions for the automatic warehouse, for which reason it is almost entirely clad in aluminium, with three-dimensional larch slat finishes, to recall the internal timber structures.
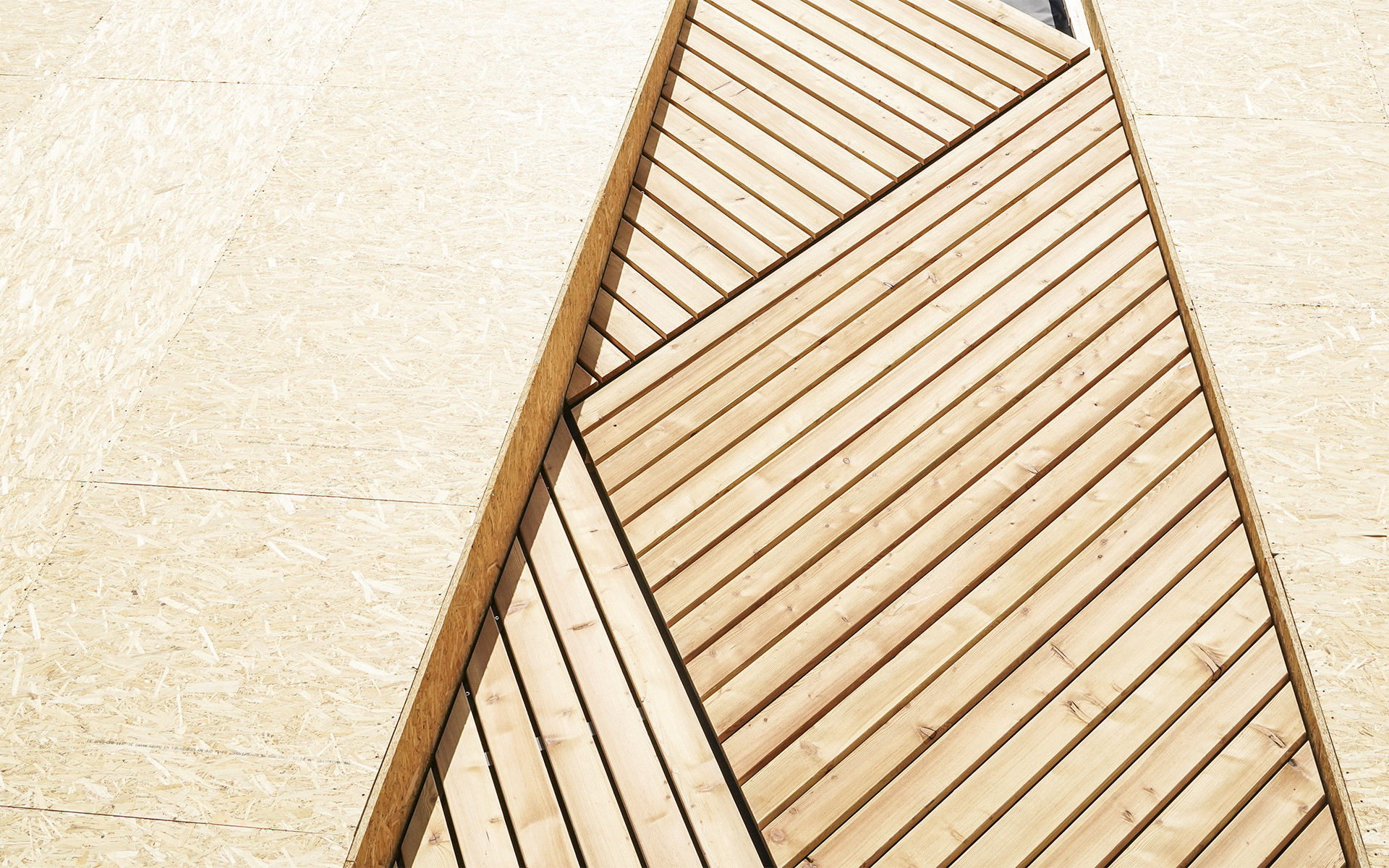
Structural concept
The special feature of a self-supporting warehouse is that the shelves, which transfer the weights of the stored goods to the ground, also act as a load-bearing structure for the warehouse itself. The main challenge for such a structure is represented by the resistance to horizontal actions (in particular, earthquake and wind).
For this, the new Rothoblaas warehouse was fitted with two independent bracing systems in the two directions. For the north-south direction (long side) twelve bracing towers consisting of a box section in LVL and glulam measuring 1 x 2.5 meters have been used. These towers were embedded in the foundation by means of plates pre-inserted in the poured concrete, and all the shelving is connected to the bracing towers in order to transfer the seismic forces onto them. In the east-west direction, the bracing system is constituted by the shelving itself, with the five hundred columns interlocked at the base and connected to each other only at the roof. The roof is constituted by a framework of glulam beams and CLT panels, which create a rigid diaphragm.
The main critical point of these structures is the deformability towards wind actions, which must be reduced in order to always allow the operation of the machines.
In fact, the project includes a displacement at the top (at a height of 20 meters) of only 19 millimetres in the east-west direction and 12 millimetres in the north-south direction.
Of course, all of the products used for the project were from Rothoblaas, but some were particularly innovative, in particular the LBS screws instead of nails and the all-thread connectors (VGZ and VGS), for extraordinarily strong fastening.
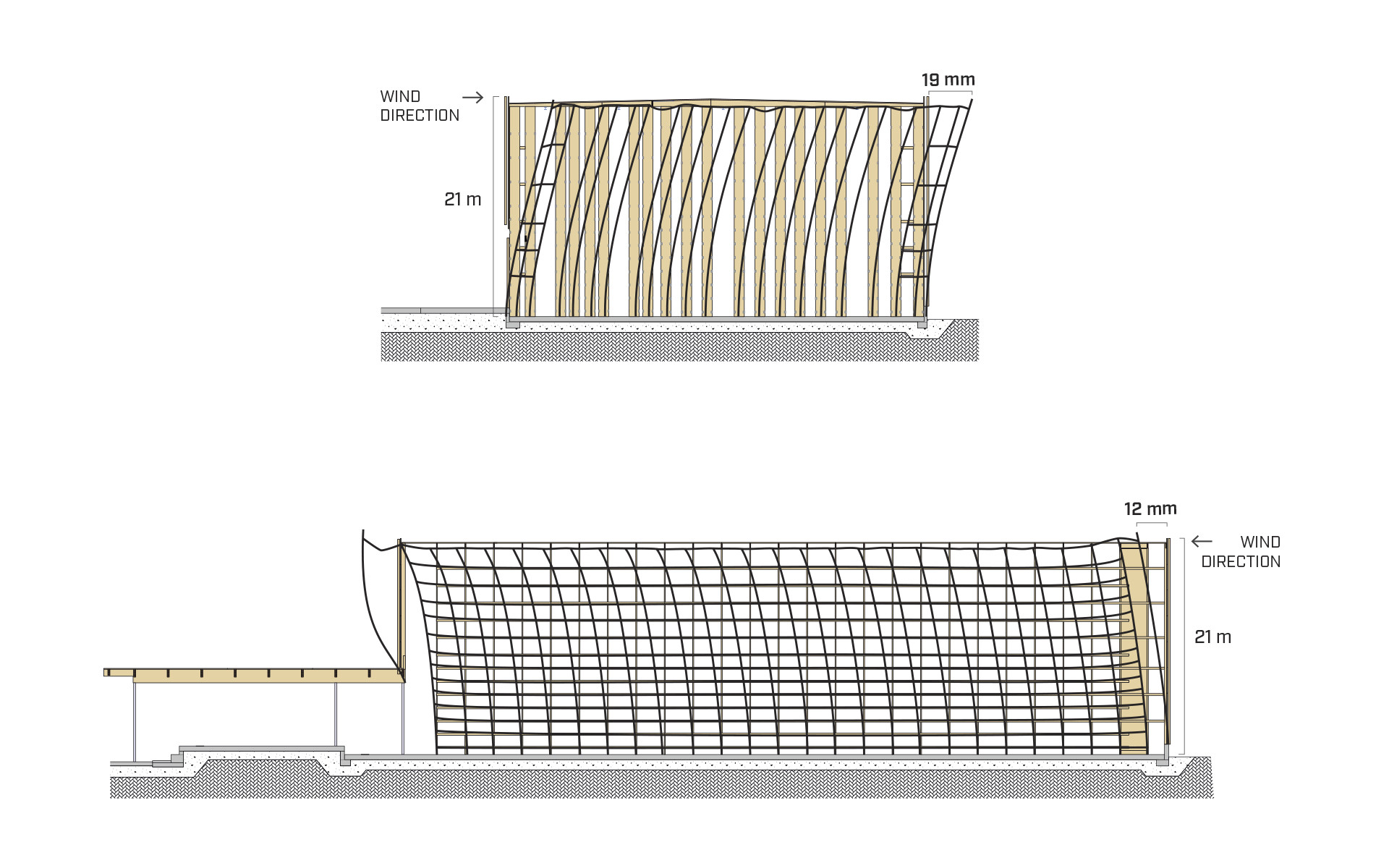
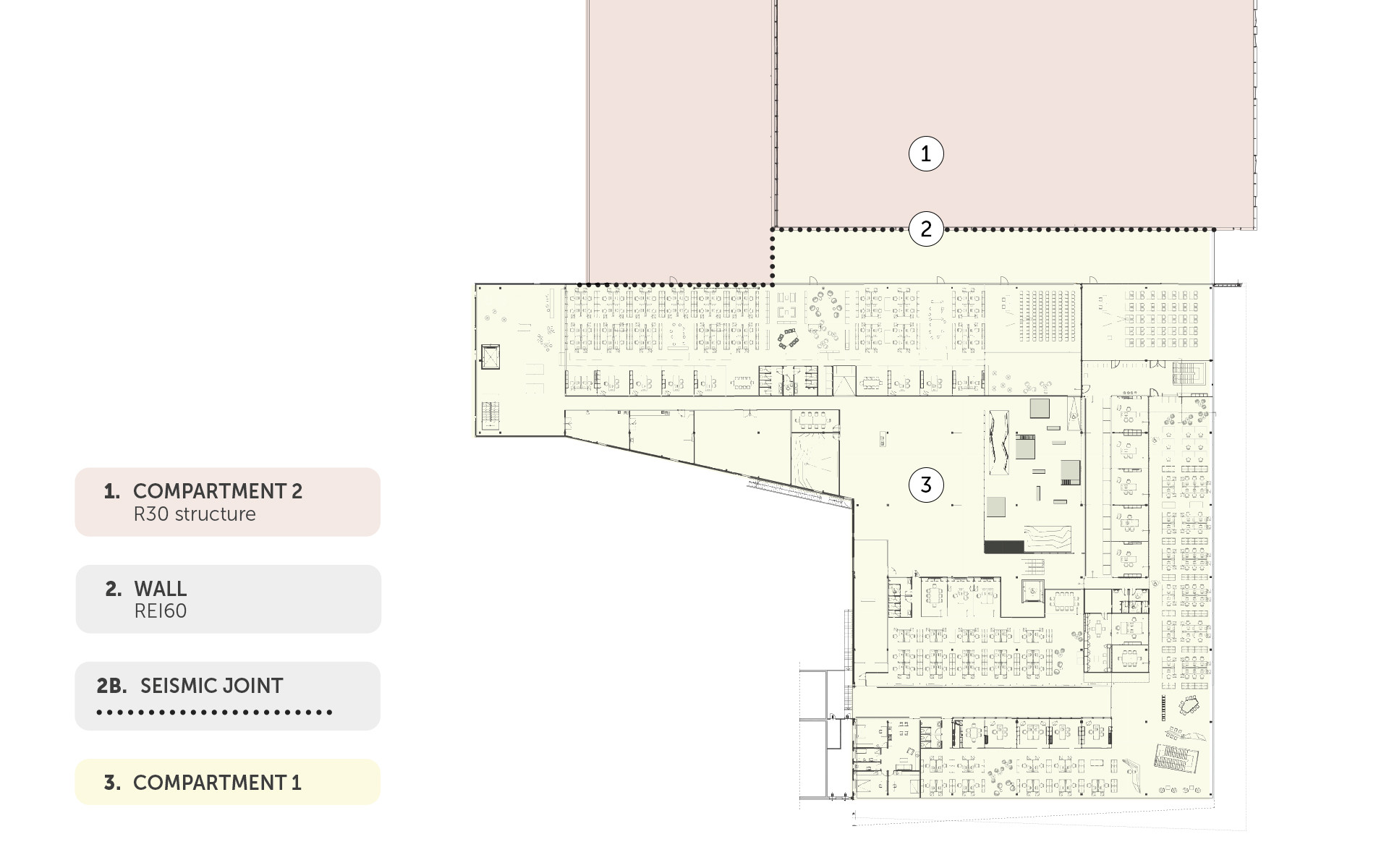
Seismic safety
The warehouse is located in Alpine territory, in an area classified as low seismic hazard. However, given the height of the building and the isostatic construction system, the design for horizontal forces (earthquake and wind) was particularly challenging. Therefore, a non dissipative design was chosen, with a structure factor of 1.5 according to EN 1998-1.
Since the building adheres to the existing building, it was necessary to create a seismic joint to decouple the dynamic behavior between old and new structures.
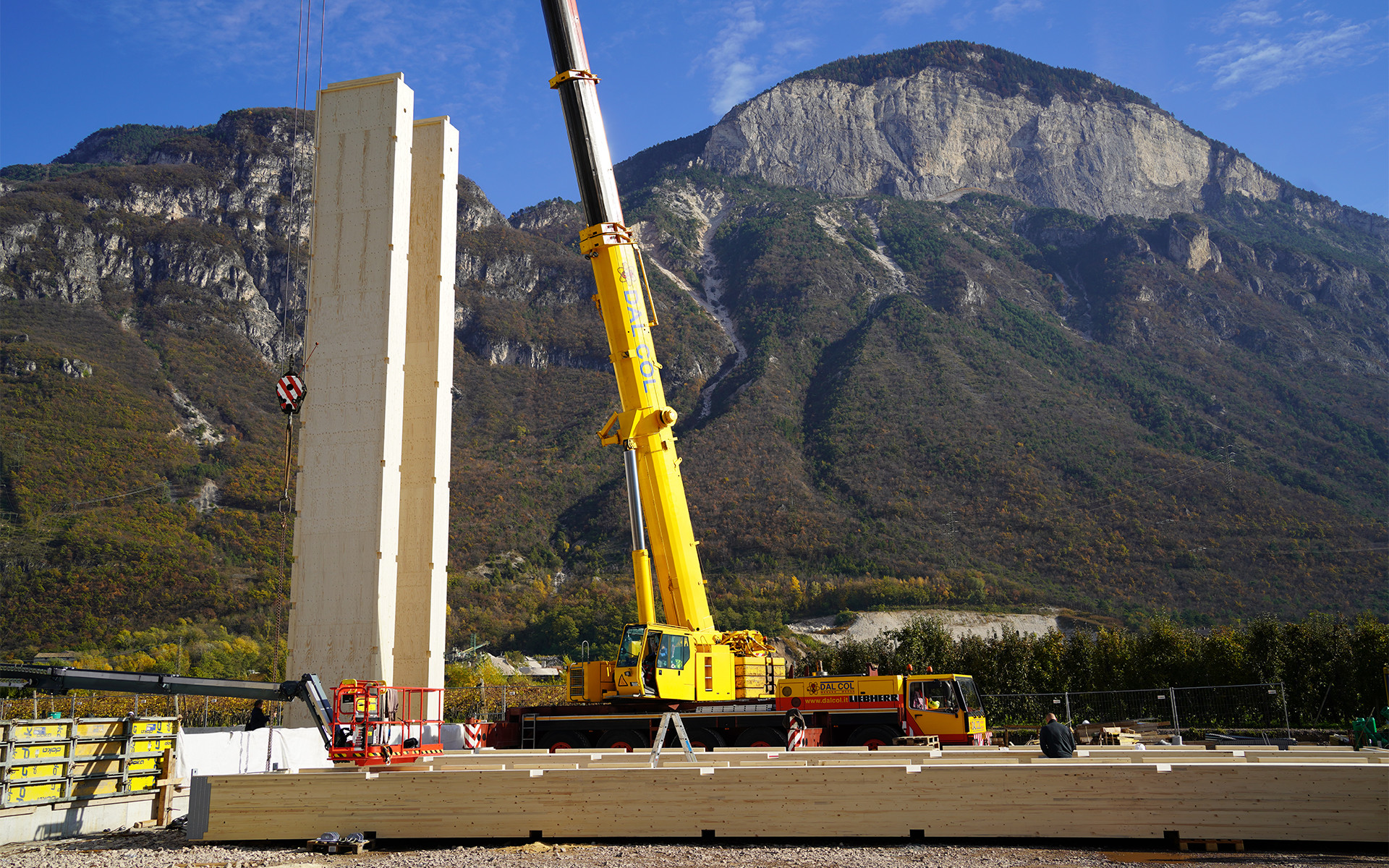
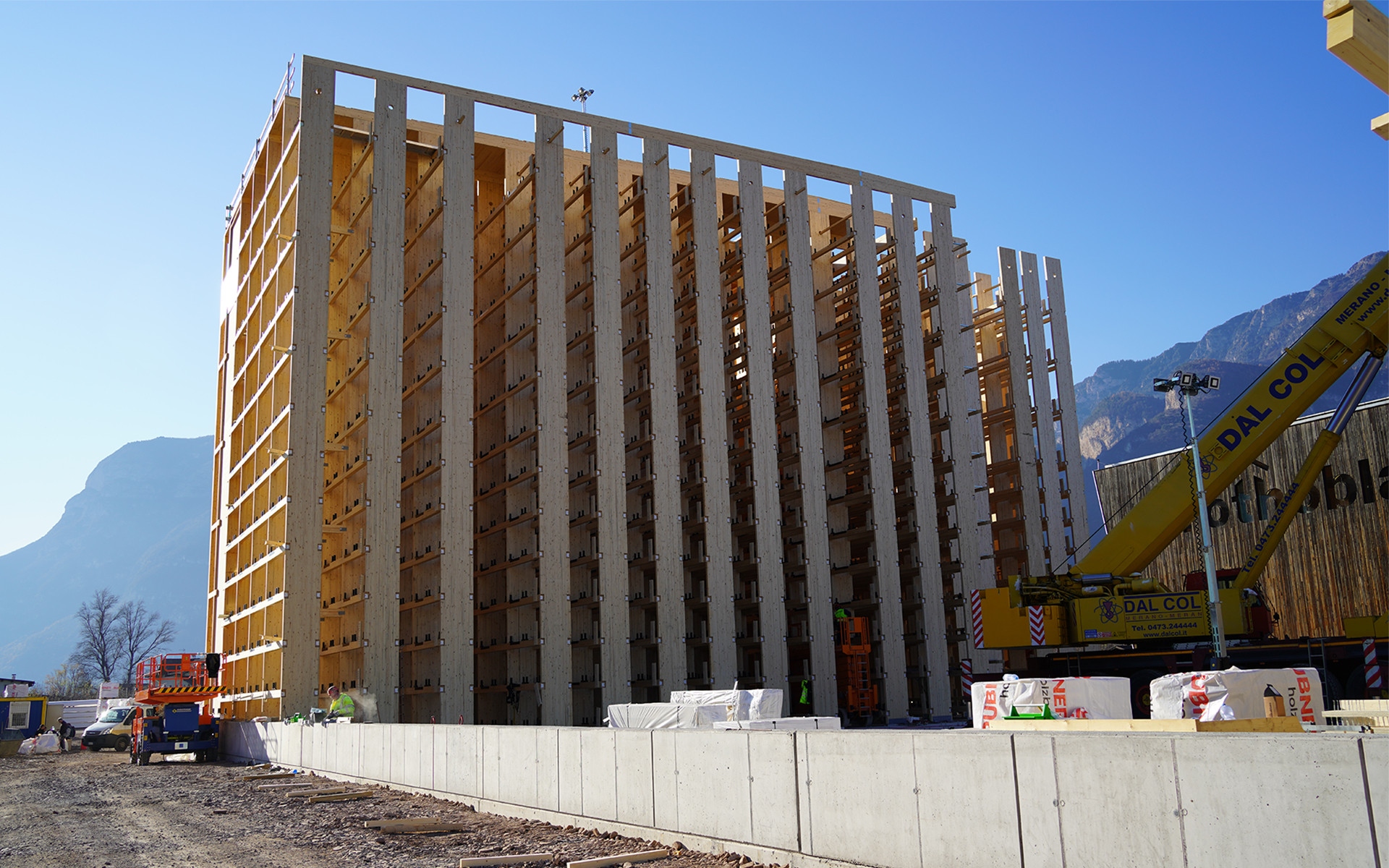
The construction site
The self-supporting warehouse, located adjacent to the headquarters, is located in the province of Bolzano, in the municipality of Cortaccia sulla Strada del Vino. The construction site is located in the former bed of the Adige River, which was reclaimed by Maria Theresa of Austria at the end of the 18th century in order to obtain land for agricultural use. This aspect had an important influence on the structural design of the foundation system, forcing the choice of a slab foundation, resting on drilled piles with a continuous helix, with a diameter of 40 centimetres and a length of 27 meters. The three hundred piles made are the roots of the forest above consisting of five hundred glulam columns, which support the shelving and the warehouse itself.
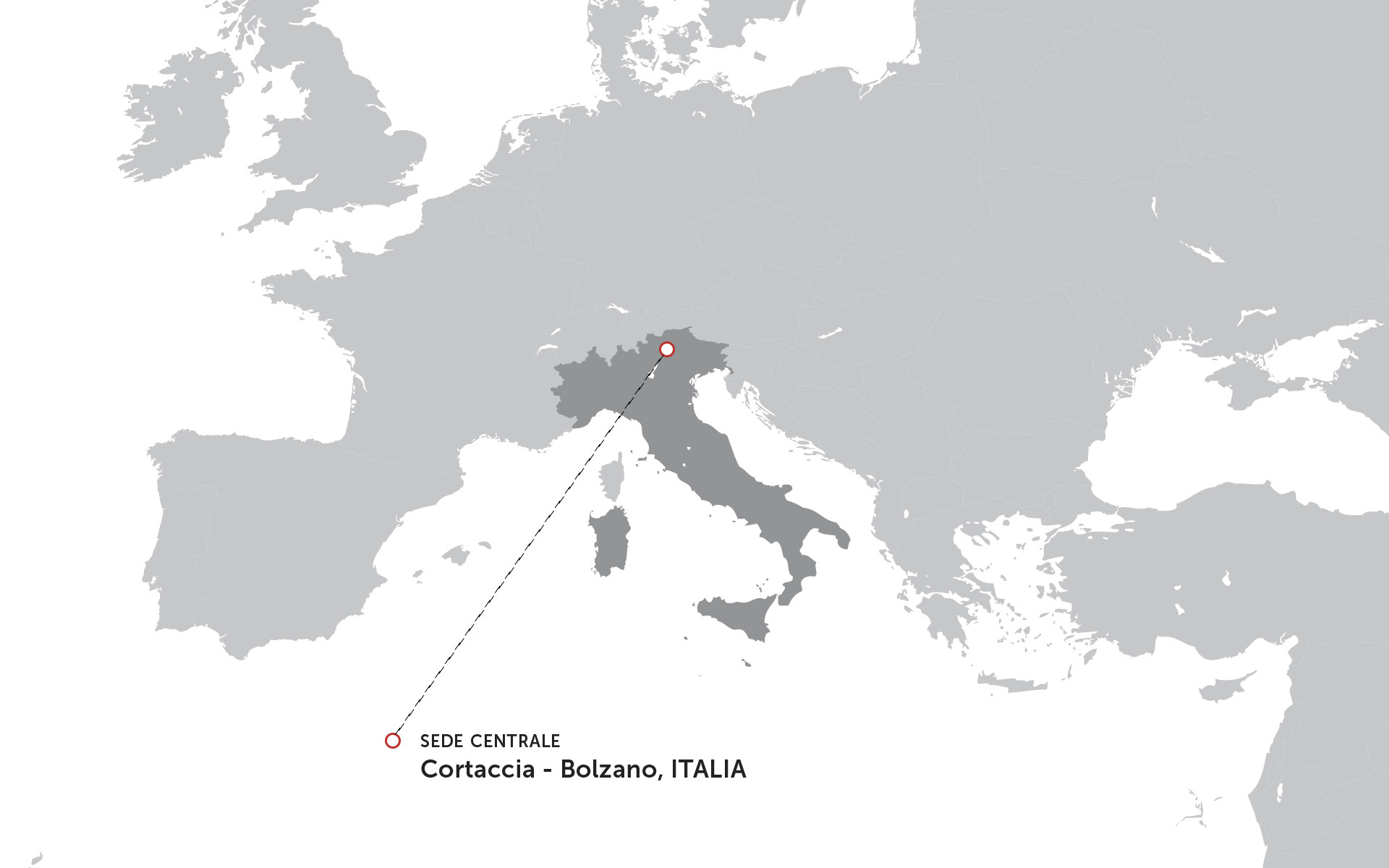
Safety for working at height and power generation
A total of 465 photovoltaic panels were installed on the roof of the automated warehouse, making the facility almost completely energy self-sufficient. The rooftop can be accessed by an outdoor ladder equipped with a vertical line, and a life line on piles has been installed for plant maintenance.
The automated warehouse systems (stacker cranes) are also equipped with vertical lifelines to allow for maintenance
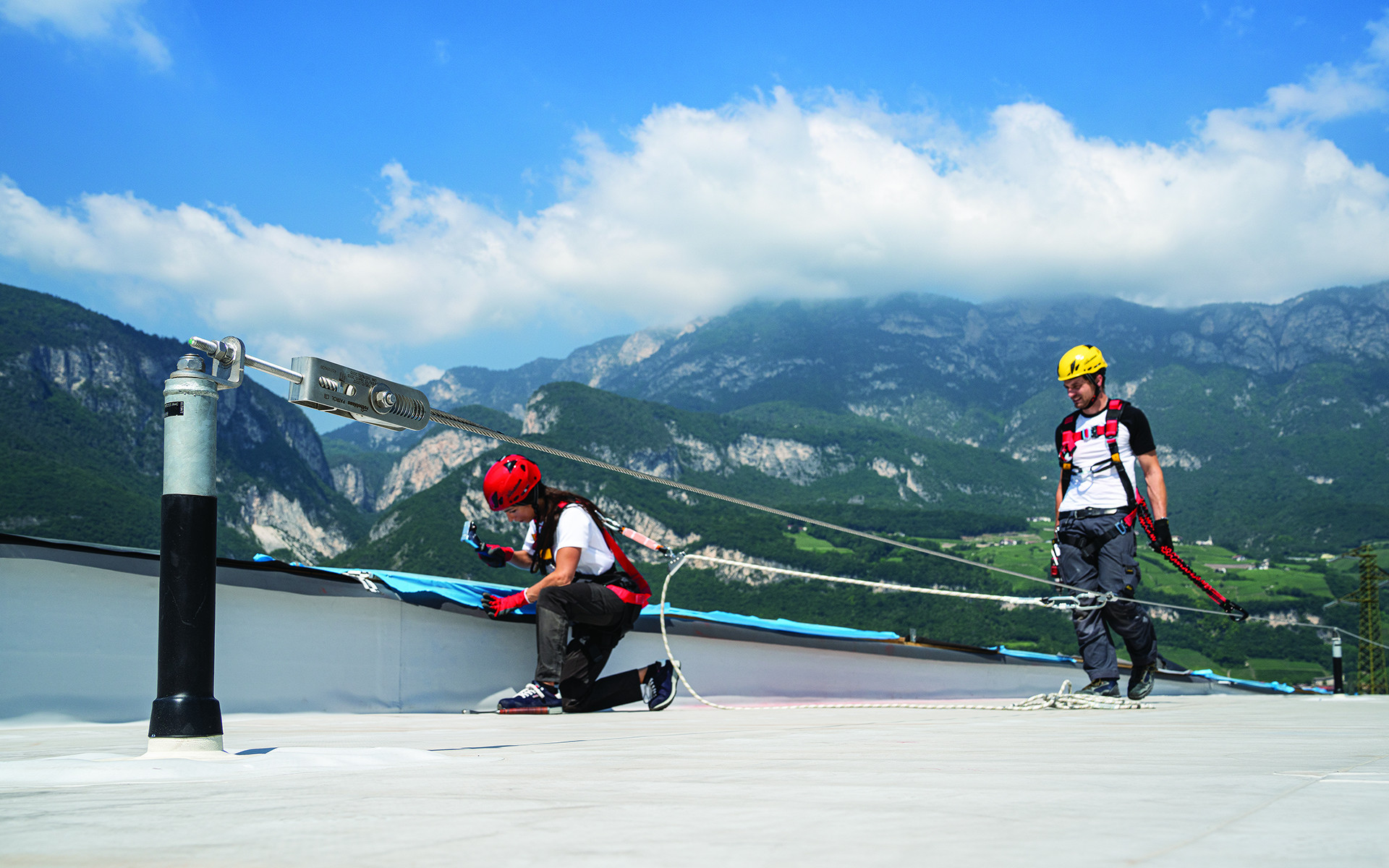
Fire safety
One of the major design challenges of the self-supporting warehouse was the structure's fire safety: various solutions were evaluated, including the use of an automatic sprinkler system, which was discarded due to the impossibility of having a sufficient water flow.
The final solution that has been adopted is therefore based on a fire resistance requirement of R30 for all the structures of the warehouse, which is relatively easy to achieve with properly designed timber structures. The R30 requirement also shifted the design of connections to solutions without exposed plates, using innovative timber-based materials instead of steel plates. Solutions with intumescent coatings to protect the steel were adopted where this was deemed unfeasible.
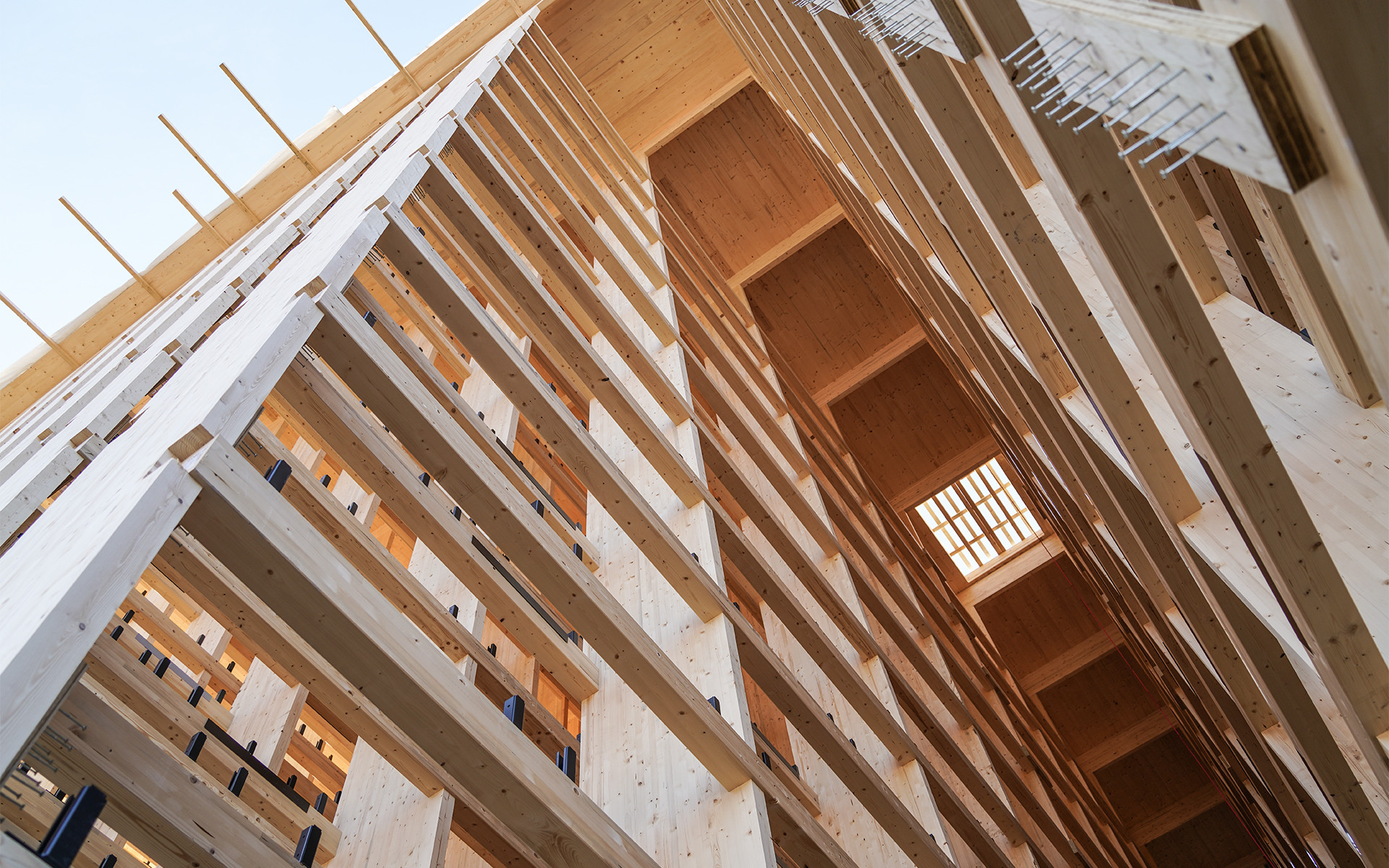
Extensions
The current headquarters, built in several steps, covers an area of 6,000 m2 and has a volume of 83,000 m3, divided between offices, warehouse and recreational areas.
The current expansion will consist of three distinct volumes as follows:
a main volume, to be used as an automatic warehouse, measuring 75 x 40 m and 21 m high;
a secondary volume, which contain the goods entrance;
an accessory volume, which connect the new warehouse with the former one.
In total, therefore, the expansion cover an area of about 4,800 m2 with a volume of about 80,000 m3.
The expansion was completed when the former warehouse was converted into open space for eighty new employees.
A tailor-made warehouse
The automatic warehouse was designed according to the company's specific needs, in relation to the materials stored and their relative weights and dimensions. Rothoblaas produces several product lines which are very heterogeneous: for example, materials such as membranes and tapes take up a lot of volume, but with a low weight, while pallets of screws or plates are smaller, but much heavier.
For this reason, the warehouse has been divided into four zones, each of which will contain pallets with different volumes and weights, with the smallest and heaviest being placed at the bottom, while the bulkiest and lightest will find space in the highest positions. Through this approach, it will be possible to reduce the effects of seismic actions on the entire structure.
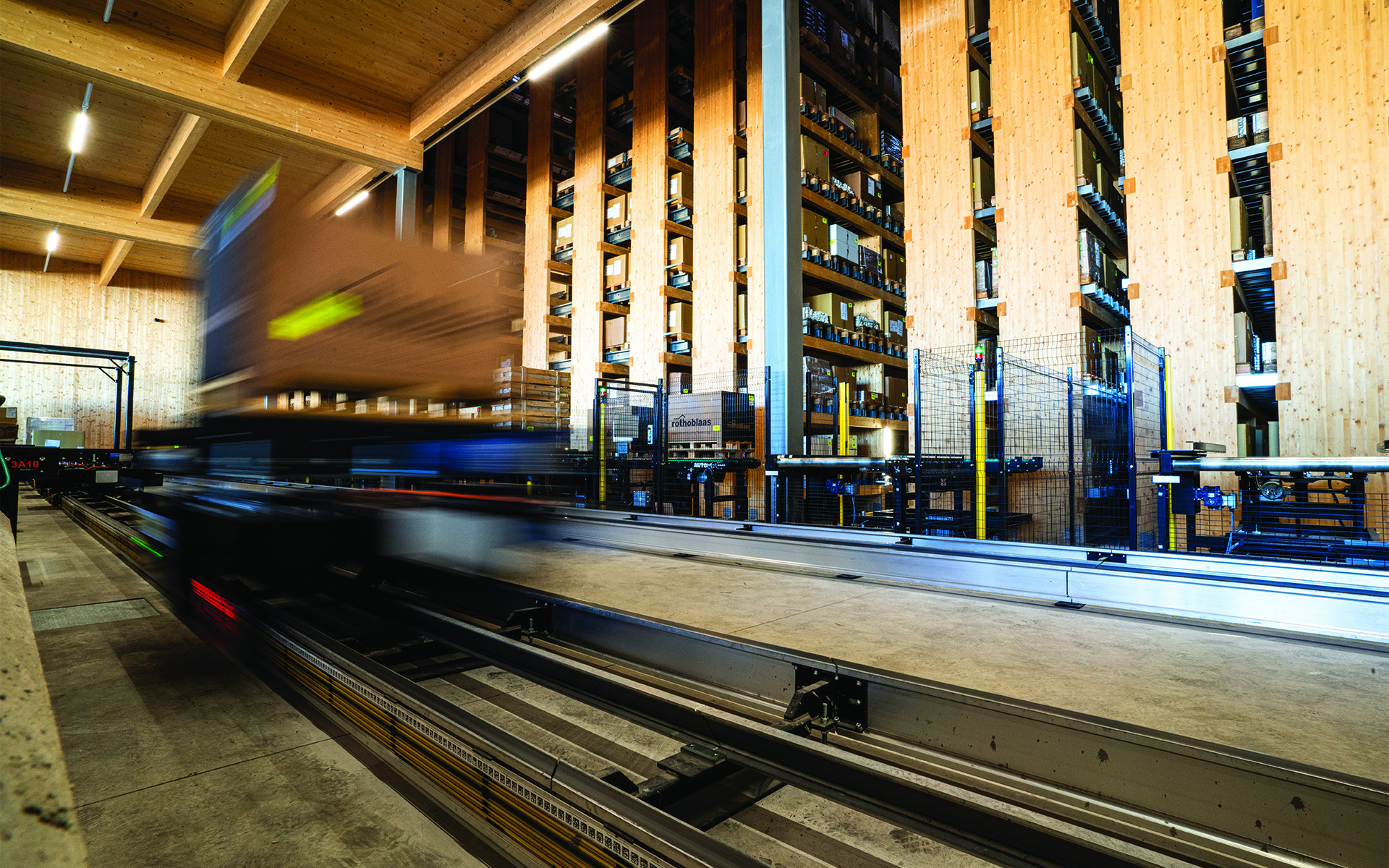
Some numbers
3.000 m3
Timber from sustainable forest management (PEFC or FSC), produced by mills within 60 kilometres of the construction site
17.000
New pallet places
2.400 tons
The use of timber allows to sequester about 2400 tons of CO2, which will remain stored in the structures until the end of its life
500 times
The 2400 tons of CO2 stored corresponds to the emission of an average car that travels 500 times around the world, equivalent to 20 million km.
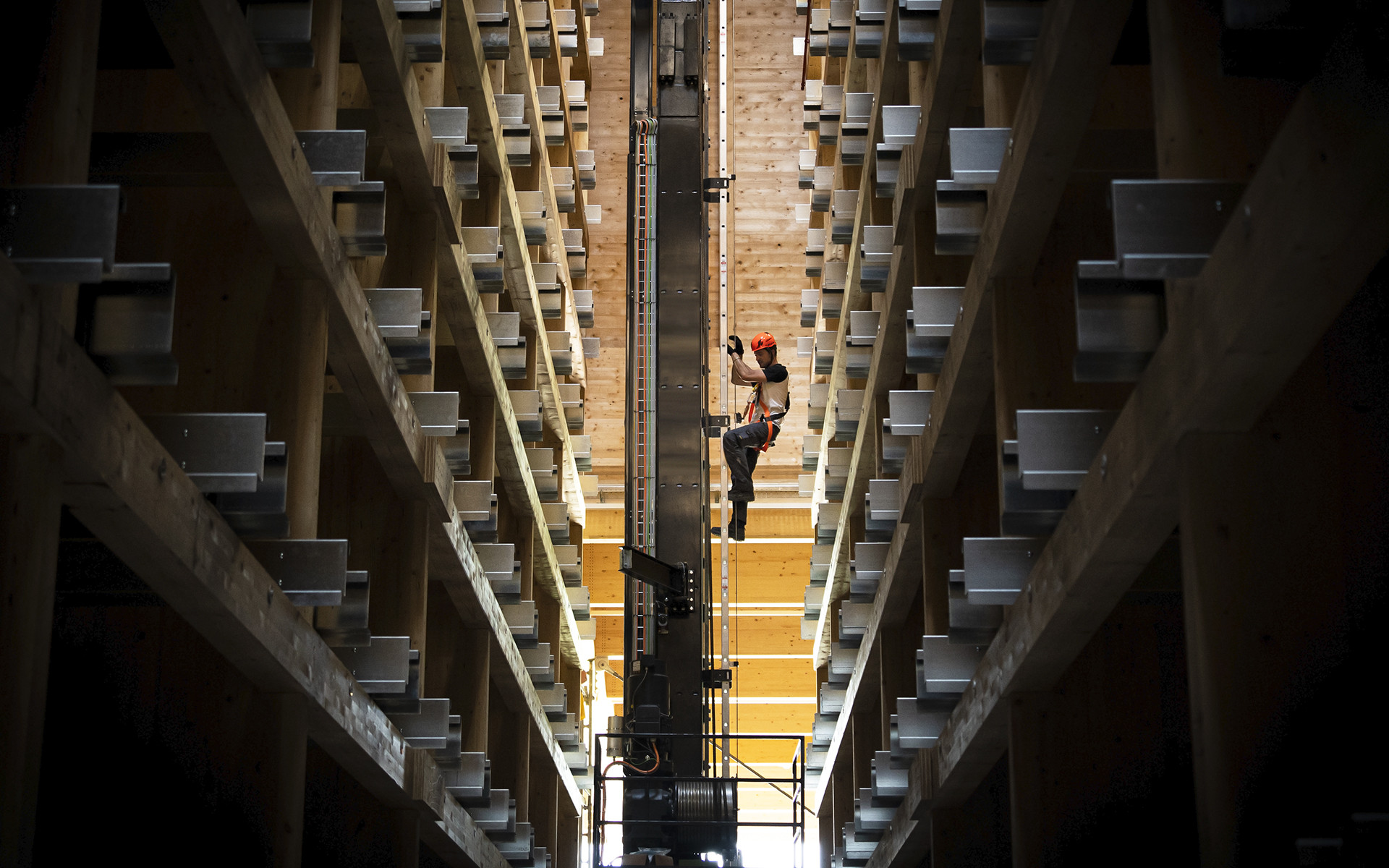
All rights reserved
Technical Details
- Year:
- 2021
- Companies:
- Studio Merz Kley Partner, Armalam, Baucon, Kaufmann Bausysteme, Arch. Lukas Burgauner, Automha, Geofondazioni Unionbau
- Country:
- Italy
- Продукция:
- LBS VGZ VGS PATROL + TOWER XL